Nothing kills laundry day momentum like a machine that refuses to cooperate. You load it up, press start, and—bam—it quits before the cycle even gets going. If your appliance stops mid-job, you’re not alone. This common issue has simple fixes, but safety comes first.
This guide walks you through 11 steps to diagnose the problem, from checking power sources to inspecting vents. We’ll start with easy solutions and escalate only if needed. Sometimes, a tripped breaker or clogged filter is the culprit. Other times, professional help is the smartest move.
Key Takeaways
- A sudden stop often points to power or airflow issues.
- Always unplug the unit before inspecting components.
- Lint buildup is a frequent offender—clean filters regularly.
- Thermal fuses and sensors may need replacement.
- Complex electrical faults require expert attention.
Introduction: Why Your Dryer Keeps Stopping
Laundry day frustration peaks when your appliance halts unexpectedly. Modern units have safety features that trigger shutdowns to prevent hazards like overheating or electrical faults. Understanding these mechanisms helps you tackle the problem efficiently.
Statistics show 1 in 3 households face drying interruptions annually. Often, lint buildup or faulty sensors disrupt the cycle. Ignoring recurring stops risks costly repairs—or worse, fire hazards.
Systematic troubleshooting is key. Start simple: check filters and vents. If issues persist, consult your manual or use a diagnostic flowchart. This methodical approach saves time and money.
For example, a clogged filter forces the machine to overwork. Safety protocols then cut power to protect components. Regular maintenance keeps your clothes drying smoothly.
1. Overheating Dryer Motor (The Most Common Culprit)
A sudden halt in your laundry routine often traces back to one key component: the motor. When it overheats, safety mechanisms kick in, shutting down the machine to prevent damage. Here’s how to spot and fix the issue.
How to Test for an Overheating Motor
Listen and sniff for clues. A buzzing noise or burning odor signals trouble. The dryer motor may also struggle to restart immediately after stopping—a classic sign of thermal overload.
Perform a restart test:
- Unplug the unit and wait 30 minutes for cooling.
- Plug it back in and start a cycle. If it runs briefly then stops, the motor is likely overheating.
Step-by-Step Motor Replacement
If testing confirms a faulty motor, follow these steps:
Symptom | Likely Cause | Action |
---|---|---|
Burning smell | Overheating | Clean lint filter, check vents |
Grinding noise | Worn bearings | Replace motor |
No restart | Thermal fuse blown | Test with multimeter |
Safety first: Always disconnect power before removing the back panel. Label wires during disassembly to avoid confusion. Match replacement motors to your brand’s specifications—universal kits may not fit.
For persistent issues, consult a pro. Electrical repairs can be hazardous without proper training.
2. Faulty Drive Belt
A loose or snapped belt can bring your laundry routine to a screeching halt. The drive belt links the motor to the drum, enabling rotation. Over time, friction causes wear tear, leading to slips or breaks.
Inspecting the Drive Belt for Damage
First, unplug the unit and remove the panel dryer (typically secured with screws). Check the belt for:
- Cracks or frayed edges
- Glossy patches (glazing from slippage)
- Misalignment around pulleys
Test tension by pressing midway—it should flex ½ inch. If loose or stiff, replacement is needed.
Replacing the Belt: A DIY Guide
- Note the belt’s routing path (refer to manual diagrams).
- Slide the old belt off pulleys and drum grooves.
- Install the new belt, ensuring proper groove orientation.
- Reattach the panel dryer and tighten screws.
Pro tip: Rotate the drum manually to verify smooth movement. If the belt slips, adjust pulley tension slightly.
3. Broken Door Latch
A faulty door latch can interrupt your drying cycle unexpectedly. The machine’s safety system detects an unsecured dryer door and stops operation to prevent accidents.
First, check alignment. Misaligned hinges or warped frames prevent the latch from engaging. Close the door and listen for a click. If it doesn’t latch, inspect for obstructions like worn weather stripping.
Use a multimeter to test continuity in the latch switch. Disconnect the harness and probe the terminals. No beep? The switch is faulty. Replacement is straightforward:
- Unplug the unit and remove screws holding the panel.
- Detach the old latch and disconnect wires.
- Install the new latch, ensuring proper alignment.
Latch Type | Compatibility | Replacement Difficulty |
---|---|---|
Magnetic | Common in newer models | Easy (no tools) |
Mechanical | Older dryers | Moderate (requires screwdriver) |
Child-lock | High-end units | Complex (professional recommended) |
Warning: Avoid temporary fixes like taping the latch. This bypasses safety features and risks overheating. If child locks conflict with the mechanism, consult your manual for disabling instructions.
4. Defective Moisture Sensor
Modern dryers rely on smart tech, but faulty sensors can disrupt the entire drying process. These components detect when clothes are dry by measuring electrical resistance. When they fail, your appliance might stop prematurely or run endlessly.
Testing Your Sensor’s Accuracy
Try the damp cloth calibration test:
- Unplug the unit and locate the moisture sensor (usually behind the drum or near the control panel).
- Wipe the metal grill with a 50/50 vinegar-water solution to remove residue.
- Place a slightly damp towel against the sensor and restart a cycle.
If the machine stops immediately, the sensor works. Continuous operation indicates a malfunction.
Sensor Type | Location | Testing Method |
---|---|---|
Bar-type | Front drum rim | Resistance check (ohmmeter) |
Pad-style | Rear bulkhead | Visual corrosion inspection |
Wire grid | Lint filter housing | Continuity test on wires |
Professional tip: Error codes like “E3” or “F5” often correlate with sensor failures. Check your manual’s diagnostic section.
Avoid bypassing the moisture sensor—this risks overheating clothes. For complex electrical repairs, consult a technician.
5. Clogged Lint Filter or Vent
Your laundry routine grinds to a halt when airflow gets blocked—here’s how to fix it. A clogged system forces the machine to overwork, triggering safety shutdowns. Left unchecked, this wastes energy and becomes a fire hazard.
The National Fire Protection Association reports 15,970 home fires annually from lint buildup. Restricted airflow raises temperatures dangerously behind your dryer back panel. Regular maintenance prevents 87% of these incidents.
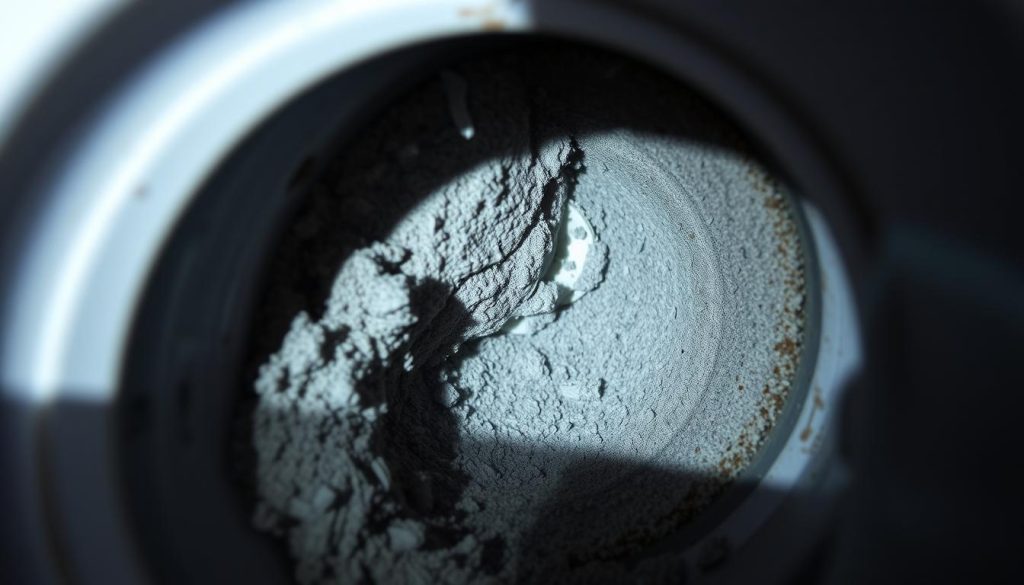
- Remove the lint filter and hold it to light—if you can’t see through, clean it.
- Feel for weak exhaust flow at the outdoor vent during operation.
- Listen for unusual whistling sounds signaling blockages.
Vent Type | Pros | Cons |
---|---|---|
Rigid metal | Best airflow | Harder to install |
Flexible foil | Easy routing | Lint traps easily |
Periscope | Space-saving | Requires frequent cleaning |
Prevent wildlife nests by installing mesh covers on exterior vents. Birds and rodents love warm, sheltered spaces. Schedule professional duct cleaning every 2 years for thorough lint removal.
Pro tip: Use a leaf blower for quick vent clearing between deep cleanings. Just detach the hose and blast air outward from the dryer back connection point.
6. Power Supply Issues
Inconsistent power can turn your laundry day into a troubleshooting session. Electrical problems often mimic mechanical failures, but solutions may be simpler than you think.
Start with basic voltage checks. Use a multimeter to test your outlet:
- Set the multimeter to AC voltage (240V for most units).
- Insert probes into the two vertical slots.
- A reading below 220V indicates insufficient power.
Safety first: Always flip the circuit breaker off before testing. Faulty wiring can deliver dangerous shocks.
NEMA Outlet Type | Voltage | Appliance Compatibility |
---|---|---|
10-30R | 120/240V | Older dryers (pre-2000) |
14-30R | 120/240V | Modern units (grounded) |
6-15R | 240V | Commercial models |
Surge protectors aren’t recommended for large appliances. They can’t handle the sustained current draw and may trigger false shutdowns.
If your circuit breaker trips repeatedly, consult an electrician. Local code may require dedicated appliance circuits to prevent overloads.
Pro tip: Test neighboring outlets too. A single faulty connection could disrupt your whole laundry room’s power.
7. Damaged Thermal Fuse
That tiny component near the heating element could be stopping your laundry mid-cycle. The thermal fuse acts as a safety switch, cutting power when temperatures exceed safe limits.
- Whirlpool: Behind the back panel near the vent
- LG: Inside the blower housing
- Samsung: Attached to the heating element bracket
Testing requires a multimeter:
- Unplug the unit and access the fuse
- Set your multimeter to continuity mode
- Touch probes to both terminals
A reading of “OL” means the fuse is blown. Replacements must match the original’s temperature rating—usually 194°F (90°C) for residential models.
Brand | Fuse Rating | Replacement Cost |
---|---|---|
GE | 194°F | $8-$15 |
Maytag | 221°F | $10-$18 |
Electrolux | 194°F | $7-$12 |
Warning: Never bypass a thermal fuse—this disables critical overheating protection. Check manufacturer websites for recalls; some models had defective fuses prone to premature failure.
For complex repairs involving wiring harnesses, consider professional assistance. Working near heating elements requires caution to prevent burns or electrical shocks.
8. Worn-Out Door Switch
Your drying cycle might stop because of a small but critical part—the door switch. This safety component cuts power if it detects an open door. When worn, it falsely triggers shutdowns mid-cycle.
Test the switch first before replacement. Unplug the unit and locate the switch near the door frame. Disconnect the harness and use a multimeter for a continuity test. No beep? The switch is faulty.
Check the plunger alignment too. If misaligned, the switch won’t engage properly. Avoid lubricating it—this attracts lint and worsens performance.
Replacement Steps
- Remove the old switch by pressing its tab or unscrewing it.
- Note the harness wiring colors for correct reconnection.
- Snap or screw the new switch into place.
Pro tip: For child-lock models, consult your manual. Some systems require bypassing safety modes during replacement.
9. Control Panel Malfunction
Your appliance’s brain might be the reason for unexpected shutdowns. The control panel manages all functions, from cycle selection to temperature settings. When it fails, your machine may stop mid-cycle or display confusing error codes.
- Capacitive buttons (touch-sensitive): Clean with rubbing alcohol if unresponsive
- Mechanical buttons (physical clicks): Check for stuck or broken components
Whirlpool® models often need a factory reset:
- Unplug for 1 minute
- Press Start + Cancel simultaneously for 5 seconds
- Reconnect power
Look for water damage indicators—white residue or discolored circuits. Spills can corrode the motherboard over time. For software issues, check manufacturer websites for firmware updates via USB.
Warning: Aftermarket control panels may lack safety certifications. Stick with OEM parts to prevent electrical hazards. If “E4” or “F7” error codes persist, professional diagnosis is recommended.
10. Overloaded Dryer
Your laundry load size directly impacts performance and safety. Packing too many clothes strains the motor and triggers automatic shutdowns. Most units handle 7-10 lbs comfortably, but bulky items reduce effective capacity.
- 1 pair jeans ≈ 1.5 lbs
- Queen sheets ≈ 3 lbs
- 10 t-shirts ≈ 5 lbs
Fabric types matter too. Heavy towels need more space than lightweight synthetics. Mixing materials helps maintain balance during spinning cycles.
Mechanical stress shows in three ways:
- Excessive vibration from uneven weight distribution
- Grinding noises indicating drum bearing wear
- Longer drying times due to restricted airflow
Brand | Max Capacity | Overload Symptoms |
---|---|---|
LG | 7.4 cu ft | Error code OE |
Whirlpool | 7.0 cu ft | Automatic pause |
Samsung | 7.5 cu ft | Beeping alarm |
Prevent overloaded situations by leaving space for items to tumble freely. When testing a load, your hand should fit between the clothes and drum roof. Regular maintenance checks keep sensors accurate for proper capacity detection.
11. When to Call a Professional
Some appliance issues go beyond DIY fixes. Knowing when to hire a professional saves time, money, and prevents safety risks. Complex electrical or gas problems often require certified expertise.
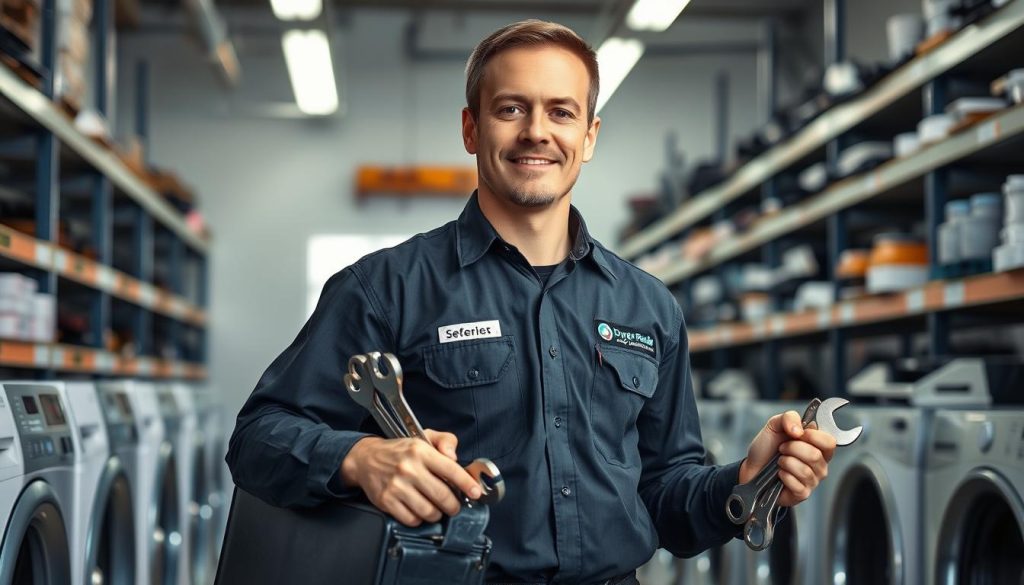
- Gas line leaks (smell rotten eggs near connections)
- Burnt wiring or sparking components
- Error codes persisting after basic troubleshooting
Manufacturer warranties may void if untrained individuals attempt repairs. Always check your coverage terms first. Authorized technicians use OEM parts and follow service protocols.
Service Type | Average Cost | Timeframe |
---|---|---|
Diagnostic fee | $50-$100 | 30-60 mins |
Motor replacement | $200-$400 | 2 hours |
Control board fix | $150-$300 | 1-3 hours |
Verify credentials before hiring. Look for:
- State-issued licenses (check online databases)
- Manufacturer certifications (brand-specific training)
- Insurance coverage (protects against damages)
Safety tip: For gas units, always request leak detection tests post-repair. Carbon monoxide detectors should run nearby during service visits.
Consider replacement if costs exceed 50% of a new unit’s price. Many professionals offer free estimates to help you decide.
Conclusion: Fixing Your Dryer for Good
Keeping your appliance running smoothly starts with smart habits. Regular maintenance and quick fixes prevent most shutdowns, saving you time and frustration.
Follow these Whirlpool®-recommended practices:
- Clean lint filters weekly and vents annually to prevent airflow blockages
- Monitor cycle times—sudden changes signal needed maintenance
- Use energy-efficient settings to reduce strain on components
For persistent issues, source OEM parts from manufacturer websites. Their support teams offer model-specific solutions.
Pro tip: Schedule annual check-ups. A small fix today avoids costly repairs later. Your laundry routine deserves reliability.
FAQ
Why does my dryer stop running after just a couple of minutes?
How can I tell if the motor is overheating?
What are the signs of a damaged drive belt?
Can a broken door latch cause my dryer to shut off?
How do I know if the moisture sensor is defective?
Could a clogged lint filter be the problem?
What power supply issues should I look for?
How do I test the thermal fuse?
When should I call a repair technician?
Related Articles: